What is warehouse management?
Warehouse management is the ability to effectively store inventory and achieve 100% fulfillment so an organization can keep pace with growing internal and external business requirements. A warehouse is the backbone of an organization’s distribution infrastructure, and when managed correctly, it will reduce operating costs and improve levels of service.
Inventory management vs. warehouse management
Inventory management is the basic approach to handling stock levels whereas warehouse management is a more comprehensive strategy that includes all aspects of running and improving warehouse operations. Inventory management is under the warehouse management umbrella, but warehouse management involves a broader focus including inbound and outbound functions, such as putaway, pick, pack and ship processes.
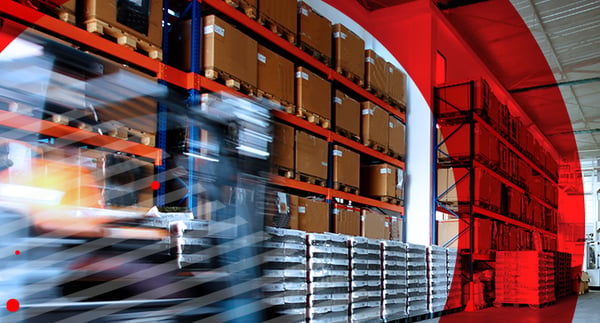
Why is warehouse management important?
Warehouse management for 3PLs
Distributors and third-party logistics providers (3PLs) are faced with competitive pressures due to higher customer expectations, higher costs and lack of available people, transportation and space resources. To combat these challenges requires an approach to warehouse management that values responsiveness, visibility and accuracy while being cost competitive. Change is reshaping the supply chain and warehouses must be able to extend, scale and adapt to support the needs of the business.
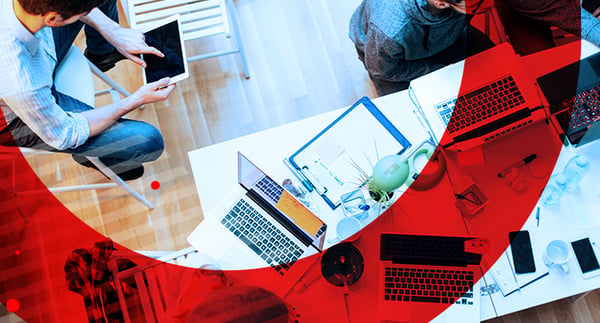
Warehouse management for e-commerce
E-commerce growth is pushing companies that were B2B entities into B2C markets and distribution. Now, rather than shipping and tracking 1,000 static orders each day, a distributor may have anywhere from 1,000 to 20,000 orders daily, from consumers who expect to receive their products within a 24-hour window. This shift represents a real opportunity, but also an innate warehouse management challenge as the B2B distribution model focuses on bulk shipments of pallets and cases while the B2C model focuses on shipping individual products.
Top 10 warehouse management best practices
-
Eliminate as many touchpoints and non-value adding operations.
-
Keep only one system of record.
-
Consolidate SKUs as much as possible and manage products from different vendors with aliases.
-
Involve vendors in operational processes.
-
Automate the input of data everywhere.
-
Get product ABC classification and slotting right.
-
Streamline picking procedures.
-
Stay on top of warehouse metrics.
-
Adhere to safety procedures.
-
Continuously strive to improve.
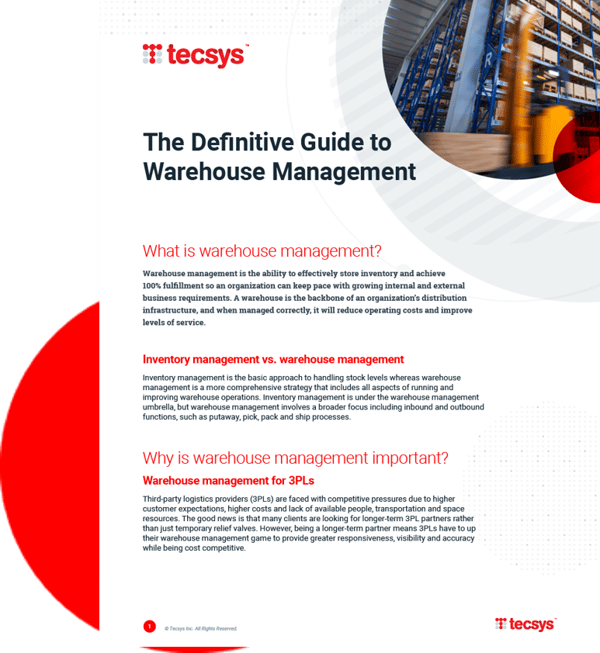
Access the definitive guide to learn the principles, strategies and solutions for effective warehouse management.
Get e-bookBenefits of warehouse management
Supply chains are often invisible to consumers, but those in charge of warehouse management know the critical role these large buildings used for storage play in everyday life. Good warehouse management provides visibility of inventory and activity in real time as it moves through the warehouse processes and enables data-driven decisions. Additionally, the space utilization in the warehouse not only ensures the best use of the storage volume, but it makes picking and packing process workflows easier for efficient and rapid order fulfillment. Ultimately, this leads to savings in labor and costs. When managed correctly, an organization can make quick and accurate decisions, attain flawless execution, deliver excellent customer service, and stay ahead of the competition.
Principles of warehouse management
Understand the key goals of the warehouse
Your warehouse needs to match your business and the first principle is to ensure the management goals within the warehouse match the goals defined by your organization. Things to consider are:
• What are your key business objectives?
• Who are your key customers?
• What are the most important goods you supply?
• Is the warehouse as efficient as it can be?
Manage your inventory levels
Inventory levels cost money and use up space; the warehouse manager needs to balance having the least inventory possible, but always having what is required by the customer. This process of managing the right inventory levels, and at the same time making sure it is in the right place within the warehouse, is the second principle and requires accurate forecasts and effective plans for resolving problems.
Control the movement of goods
The layout of the facility and the location of the goods within the facility all help in controlling the movement of goods within the warehouse. This principle is really the process of traveling the least distance possible to perform the most work possible.
Make quality a key target
Efficiency and optimization are only valuable if the work is accurate and quality has to be the first and foremost goal of the workers in the warehouse. Creating workflows that drive quality and self-correcting processes throughout the facility ensure the quality of work within the warehouse.
Pick the right WMS software and partner
Your warehouse management system (WMS) will either help or hinder your drive to the previous principles. Getting the right technology and right technology partner to run your warehouse will make things far more simple and attainable.
How to gain efficiency in the warehouse
The critical factor with gaining warehouse efficiency is understanding both the usage and availability of your space.
Getting a handle on the size of your warehouse and the sizes of all your products will allow you to drive efficiency.
• Attain accurate cube data on all your items and units of measure.
• Get accurate cube data on all the locations in your warehouse — this does not mean the dimensions, but the actual usable space of each location.
• Ensure your putaway process allows for flexible inventory placement.
• Consider the cube of the items when performing ABC slotting.
• Manage your cross docking and order staging with an eye to the dimensions of the goods.
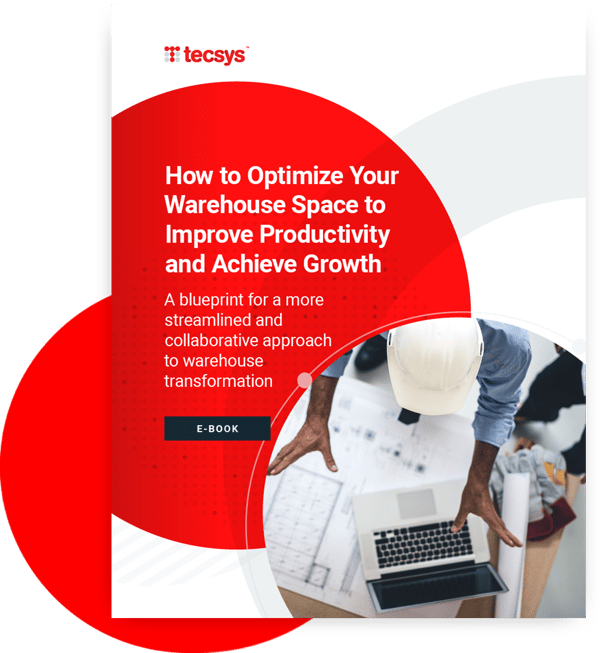
Access this e-book to learn about the advantages of a modern warehouse design process and the value of participation from all relevant parties.
Get e-book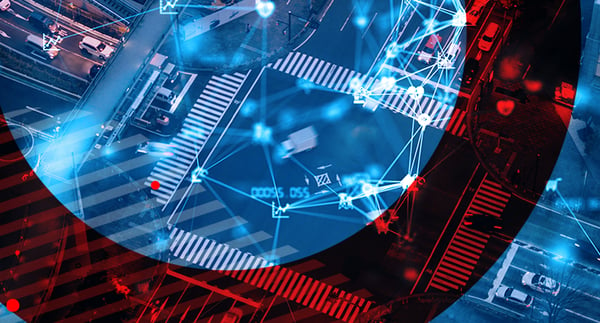
What is a warehouse management system?
A well-designed warehouse management system will optimize the flow of materials through your various warehouses, managing the processes that are required to move the goods from inbound receiving, through storage and retrieval, and ultimately to outbound picking of customer orders. The WMS is connected to the enterprise resource planning system (ERP) or order management system (OMS) to receive customer and purchase orders which are used as a checklist of goods expected to arrive into the warehouse or pulled from the warehouse.
What does a warehouse management system do?
At its simplest level, a warehouse management system utilizing mobile technology will lead an operator through the process of moving goods from place to place within the warehouse. The technology behind the WMS will attempt to do this in the most effective and efficient way, while making sure the operator makes zero errors during the process. In addition, the WMS will track and record the goods already in the warehouse to make sure they are being stored in the proper locations and consumed in the correct sequence.
Take for example a warehouse that serves a mid-sized distributor of hard goods; throughout the process of managing the warehouse there are decisions that must be made and critical instructions that must be followed. A WMS will track and manage these processes while ensuring 100% accuracy with the least amount of labor.
Receipt
This is the process of when goods arrive at the warehouse shipping dock. A WMS will efficiently help determine and confirm the right product, in the right quantities, in the right condition, weight and dimensions all at the right time.
Putaway
The objective is to move goods received to an optimal storage location as quickly and efficiently as possible. During the putaway process a WMS considers different factors (e.g., if the goods need refrigeration, if there is an order already waiting for the goods, etc.) and calculates the location and best possible route to take when putting away the items.
Storage
This is a critical process to ensure all available space in the warehouse is maximized without compromising productivity. A WMS tracks if goods are in the best location, if the amount of goods is accurate or if a reorder is necessary, if the goods have expired, etc.
Picking
This is the process used to retrieve goods in the warehouse and consists of picking by item, group or zone. The WMS communicates and controls the picking task by providing explicit direction to the pick person via mobile data devices, interactive voice and pick-to-light modules, and by controlling the quality of results with various forms of automatic identification (e.g., barcode scanning, etc.). Directions will include details such as how many to pick, what type of pack size is best to pick, which lot number to pick and if the item requires pre-work (e.g., price labeling, tagging, assembly or similar).
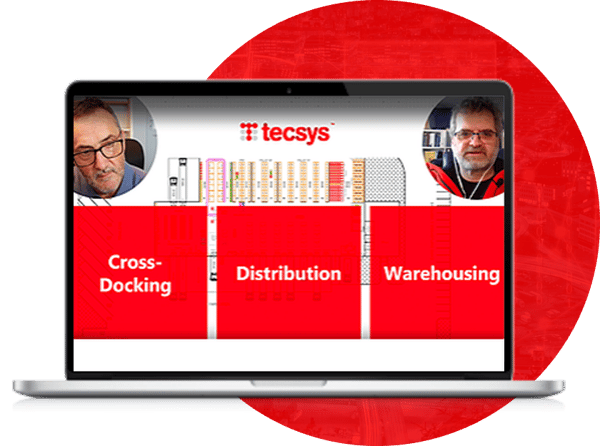
Get your consultation on how to optimize your warehouse from a WMS specialist with more than 30 years' experience.
Watch WebinarHow does a warehouse management system fit in the supply chain?
A warehouse management system performs three key functions for the supply chain: cross-docking, distribution and warehousing. Balancing these three warehouse management functions creates an efficient supply chain operation and enables you to adapt to customer demands.
Types of warehouse management systems
Warehouse management systems can be divided into three types: the standalone warehouse system, the ERP module and the best-of-breed warehouse management system.
Why are companies upgrading their warehouse management systems?
You may hear about warehouse management system upgrade projects and wonder when the right time is to move your existing WMS to the latest version. If you are running a traditional system, the time may be right for you to explore the more modern options now available for your operations.
Below are some common reasons a business will upgrade. These are often determined by developing a business case that fully explores all aspects of the business and future expectations from customers.
• The cost of staying on the current system is higher than it would be to move to a new system.
• The current system is now restrictive and cannot support organizational growth.
• The current system is not effectively serving existing customers or helping to win new business.
• The investment in a new system will support innovation and the opportunity to be more competitive in the
marketplace.
The pivotal role of the warehouse management system
The WMS plays a crucial role in enabling your organization to complete daily activities spanning from receiving, putaway and inventory management to picking, packing and shipping — and much more. Anything less than a robust WMS will hinder your ability to grow and serve customers effectively.
Unfortunately, many decision makers delay the move to a best-of-breed warehouse management system because of the perceived disruption these projects can cause. A feature-rich WMS can certainly involve an extensive amount of work to develop processes, configure the software, integrate with your enterprise systems, prepare the IT infrastructure and execute testing plans. However, delaying the move to the right technology in turn can postpone responding to customers’ needs, revenue-generating growth and the competitiveness of your business in the market.
Some companies have elected to implement “WMS light” options designed with a reduced feature set. However, these typically do not allow for the type of growth and the associated complexity in distribution requirements these companies may ultimately require.
Cross-docking
This is the management of goods in the warehouse that are received and shipped within a very short timeframe. There is usually little to no on-hand inventory and the focus of a cross-docking operation is to eliminate storage and retrieval tasks. This is applicable to the initial receipt of seasonal items, non-stock or pass-through items and backordered items. The WMS helps ensure the product is received and staged for shipping in as few steps as possible.
Distribution
This is the management of goods that have relatively low inventory levels and a high turn rate. The focus of a distribution center operation is satisfying customer orders as efficiently as possible while holding the least inventory. The WMS simplifies the order picker’s job by using appropriately sized and identified picking locations. Overstock is usually kept near pick locations and there is an emphasis on the optimum slotting of items.
Warehousing
This is controlling stock items with high inventory levels and a low turn rate. The focus of a warehouse operation is to maximize storage capacity and typically has a low SKU count, but high inventory levels. The WMS orchestrates the product (e.g., imported items, emergency use items, production operation goods, etc.) from receipt to storage in high-capacity locations.
Succeeding in a challenging distribution environment
Simply put, it is not always easy to achieve highly effective distribution operations in today’s fast-paced environment. Customer expectations are exceptionally high in the era of the “Amazon effect,” when fulfillment cycles and delivery times must be continually compressed. This is because consumer expectations for expedited delivery have become the norm on the B2B side as well, placing untold pressures on global supply chains.
Exceptional warehouse management is the key to growth and long-term success. This is possible through the right approach to technology, which includes any necessary material handling equipment as well as a proven, feature-rich warehouse management system. Only with effective systems underpinning your operations can you process the growing volumes of orders, manage inventory and ensure your associates carry out each step of their directed tasks properly every minute of the day. Accuracy and reliability are essential. There isn’t any room for error if you want to stay competitive.
"In today’s warehouse operations, we see more business volumes, more goods to move to multiple channels, under tighter cycle times. Combined with labor shortages and stringent regulatory requirements, the pressure on executives is greater than ever! As a result, they have no alternative but to make a technology change to a robust and flexible WMS to keep up with their changing business requirements. Given their business conditions, they need to do it at low-risk and low-cost, in other words, get top WMS value at a low total cost of ownership. – Michael Mikitka, CEO of WERC (Warehousing Education Research Council)"
3 reasons to leverage a warehouse management system
Given the complexities of the supply chain today, there are several important elements to consider when selecting the right technology for your business. Zeroing in on the right warehouse management system is a career-defining decision. You must take a thorough approach in your decision-making process by evaluating your challenges, requirements, budgetary constraints, expectations and the range of options available.
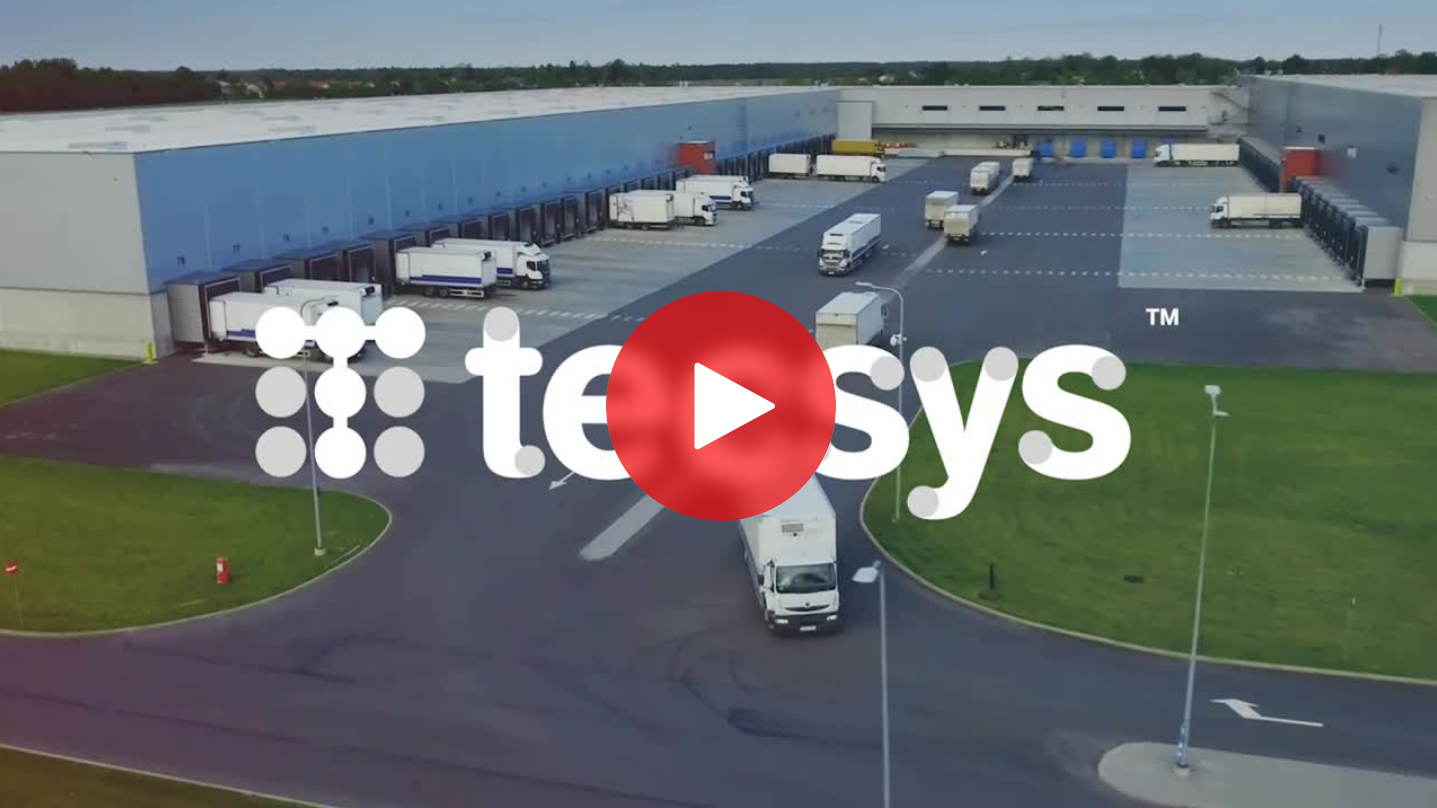
1. Functionality
It is essential to have a warehouse that is scalable and easily adaptable to your specific needs, market conditions or unique customer requests. A top-notch WMS will have core warehouse features that go beyond the standard options such as receiving, putaway, counting, letdown and picking. While these remain important capabilities, you need functionality that enables you to meet industry-specific requirements such as value-added services; full lot, serial and expiration track/trace and many more that will enter the picture as appropriate.
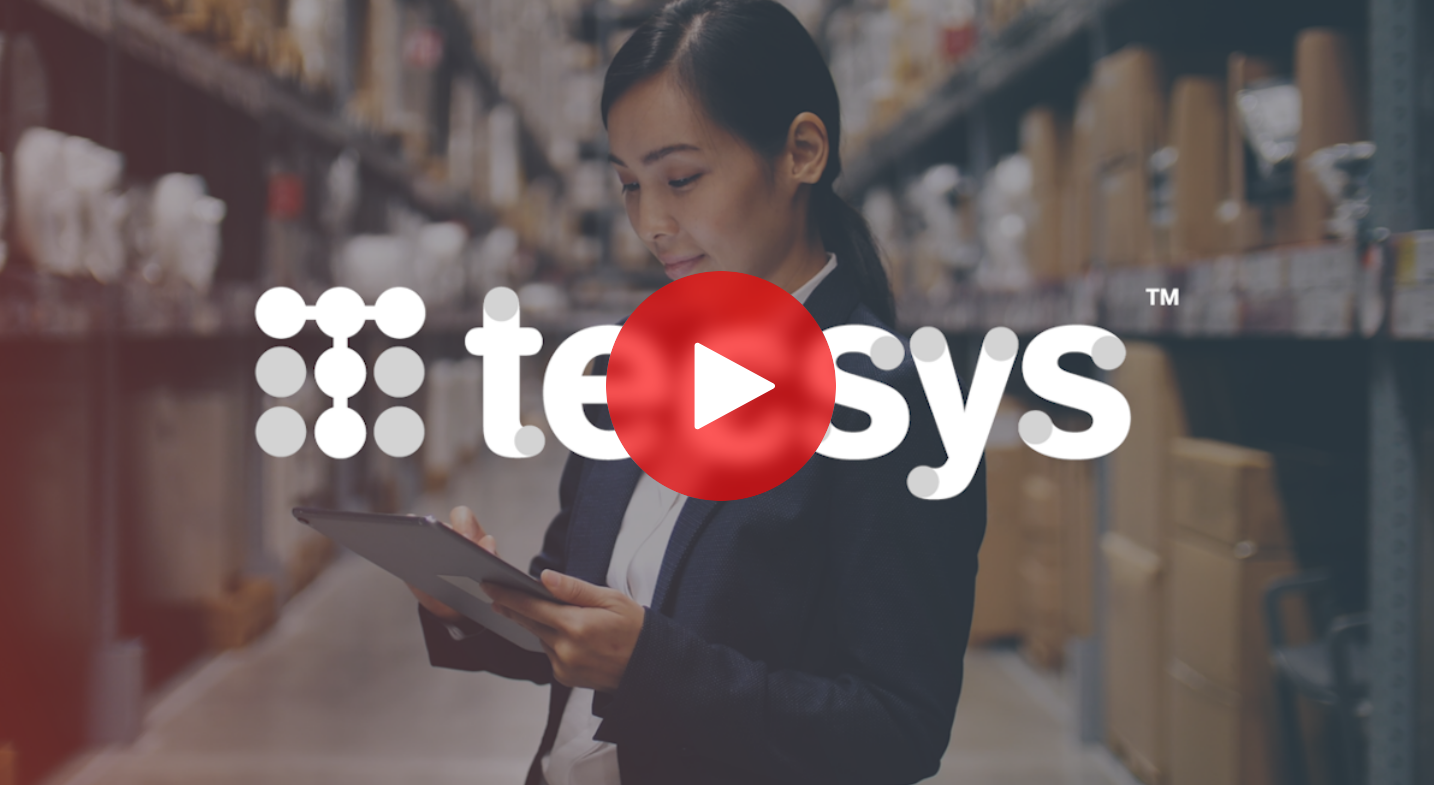
2. User experience
Labor is a critical element to a warehouse and it is important to provide workers with highly intuitive technology to help them be as efficient as possible – right out of the gate. The WMS should be easily understood with step-by-step instructions and visual cues to ensure accuracy and compliance. Particularly if temporary or seasonal workers are important for your business, technology that is easy to adopt with minimal training will be the key to success.
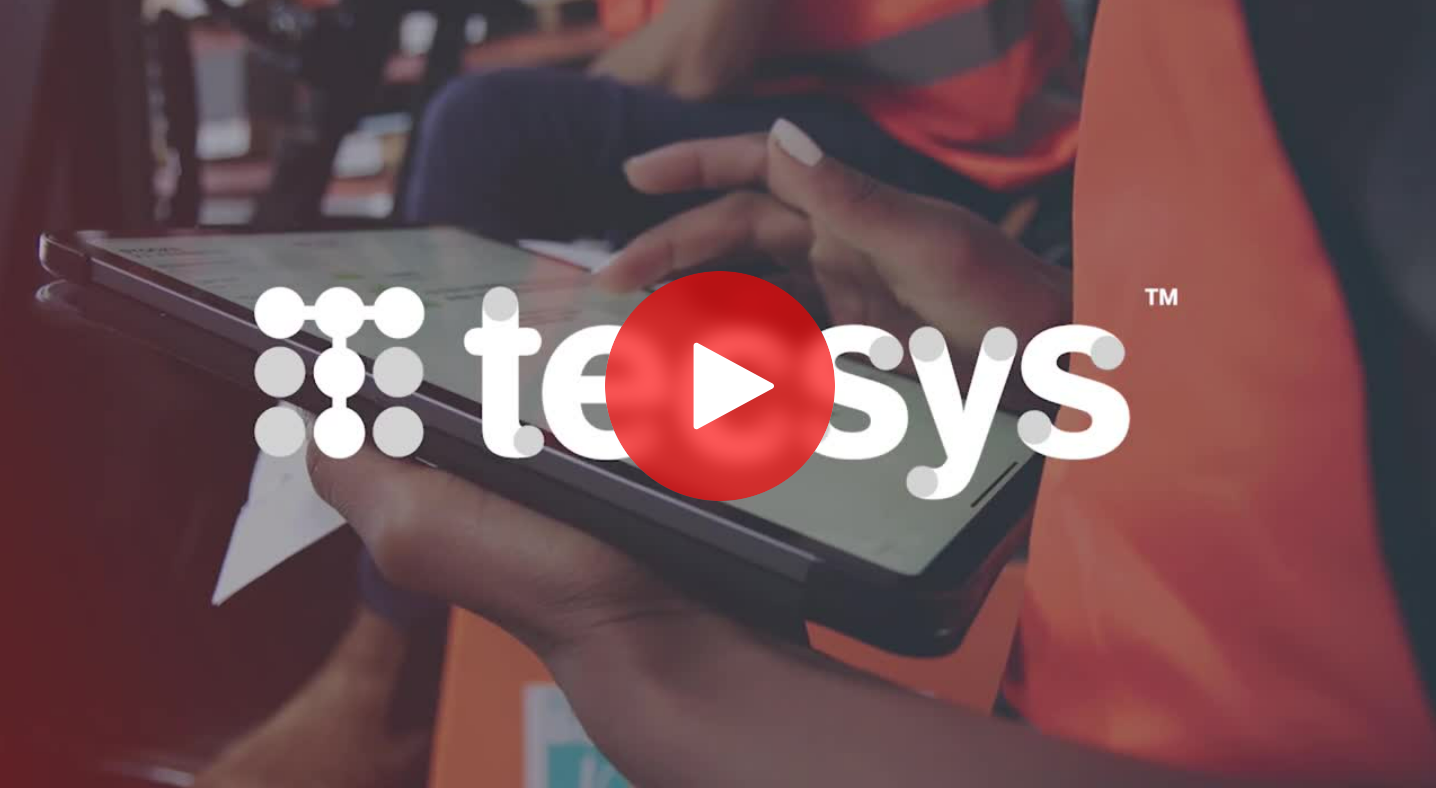
3. Flexibility
The way your warehouse operates today might not be the same way it needs to operate in the next few years. Many companies are making increasing use of cloud deployments to ensure the flexibility of their supply chain. A WMS can scale and adapt automatically with elastic technologies and tools that are secure and continuously upgraded to meet the needs of your industry and business.
Features of warehouse management systems
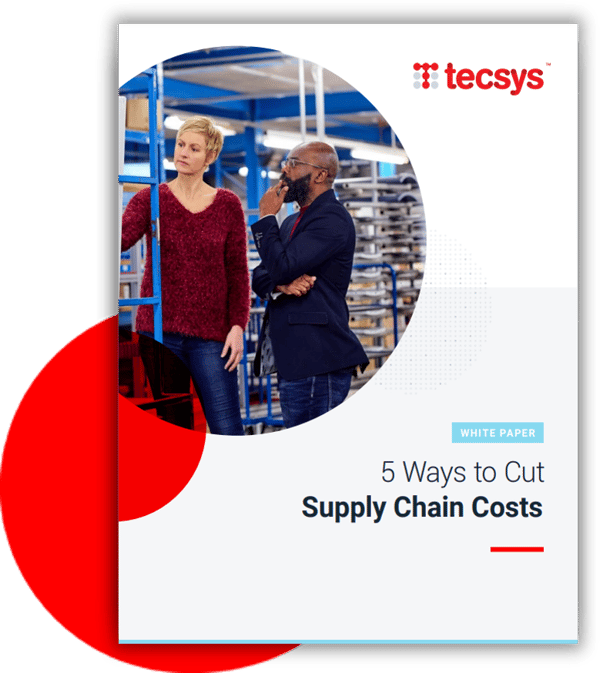
Find out five ways to cut supply chain costs through new approaches to efficiency and visibility
get white paper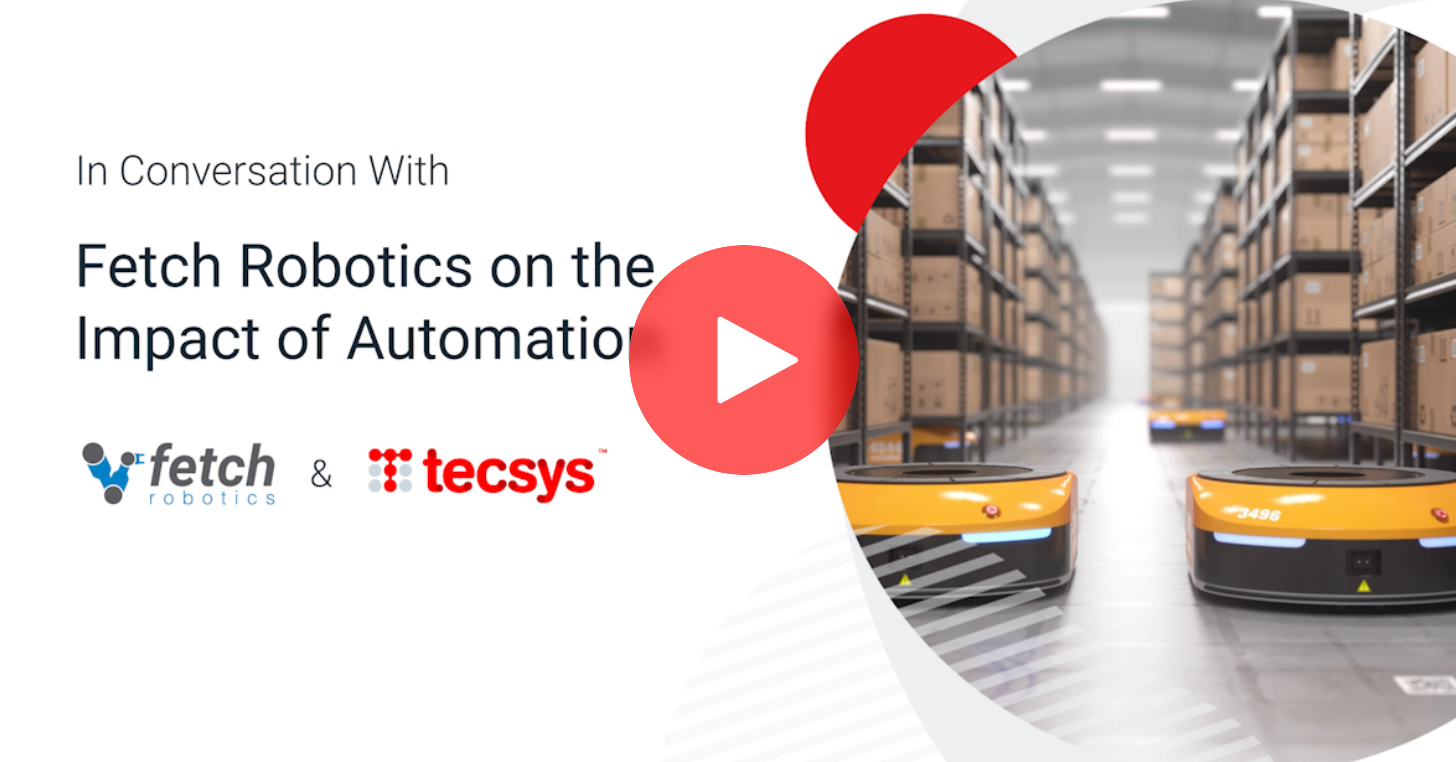
Ways a modern warehouse management system helps reduce costs.
Automates manual processes
From receiving, putaway and inventory management to picking, packing and shipping, there are many ways you can leverage automation to forego routine, manual processes. Assess your operations and determine where the lowhanging fruit resides when it comes to what to automate first. A good place to start are the repeatable and timeintensive activities, especially those prone to error. Do not forget to evaluate material handling equipment (MHE) that can integrate with your warehouse management system to speed operations. Conveyors, pick-to-light systems, automatic guided vehicles (AGVs), automated storage and retrieval systems (AS/RS) and more not only help your workers complete assignments faster, but they can also improve safety and take the physical burden out of some of the steps.
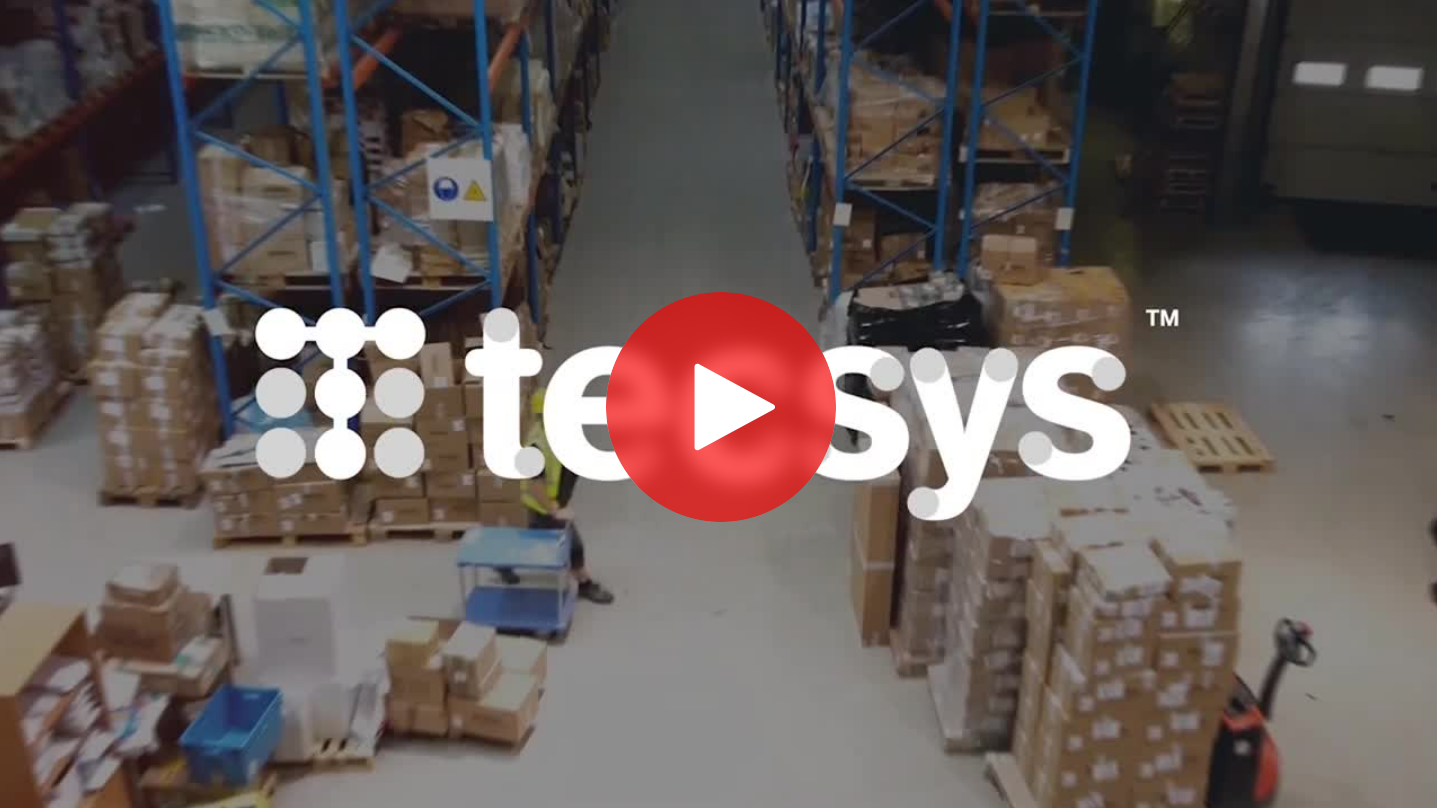
Enhances workforce efficiency
Finding and retaining a solid workforce is a growing challenge for many companies. A warehouse management system that is easy to work with and simplifies the process of completing tasks accurately will make a world of difference in your ability to hire, train and retain staff. If you are able to introduce automation as mentioned above, you may find you can carry out the same tasks with fewer associates. However, this does not necessarily mean you have to let workers go. It is feasible to offer additional training to some associates and redeploy them to other areas where performance may be an issue. You can also use newfound employee bandwidth to implement offerings such as personalized, value-added services that delight your customers.
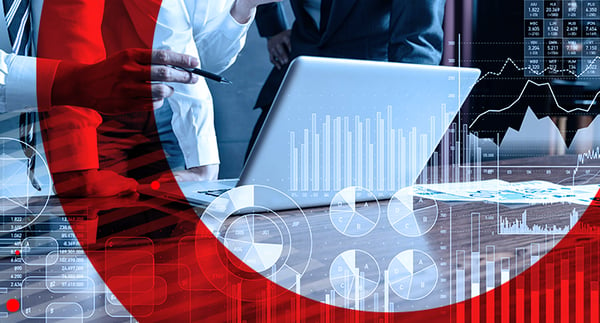
Optimizes inventory management
Having too much inventory, not having enough or lacking the right kind of inventory all create financial stress and customer service challenges for your organization. The first requirement to improving inventory management and lowering your holding costs is having visibility into what is on the shelves and the rate at which it is depleted and replenished. This is possible with a warehouse management system in concert with an inventory management system that tracks the ins and outs as well as prompts cycle counting and reconciliation. The ability to forecast demand is also an important step as you work to implement an optimum level of inventory to carry and lower inventory holding costs over time.
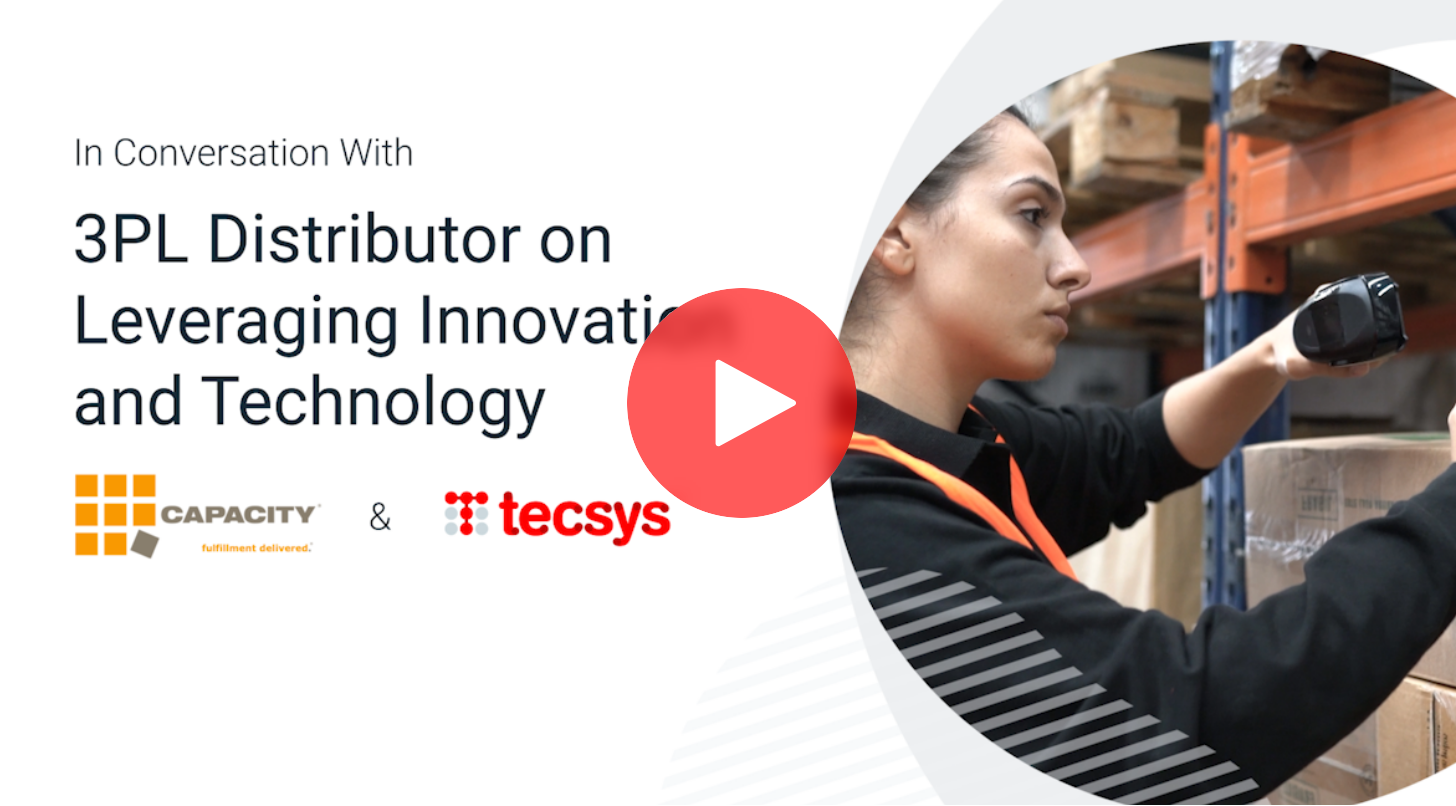
Enables best practice implementation
Although supply chain experts have been developing best practices for decades, recent changes in distribution models, technology and customer expectations have led to new insights into the best ways to run distribution operations. A warehouse management system provider has a deep understanding of supply chain best practices and can introduce efficiency into your distribution operation. Learn the latest best practices regarding facility layout, how to leverage technology and manage your workforce in pursuit of meeting customer requirements and keeping costs in check.
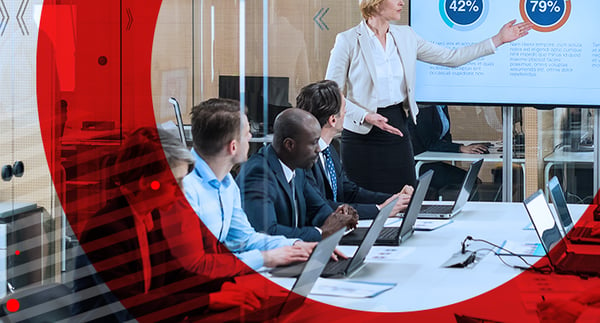
Measures performance
Best-in-class distribution operations of any size rely on accurate metrics and analytics for informed decision-making. From labor productivity to fulfillment speed and shipping accuracy, intuitive WMS dashboards will help you get a handle on which areas are not running efficiently, where cost spikes point to underlying issues and more. What you seek is information that can help you take action, enabling ongoing improvement and cost reduction across many areas. This may include dropping a product line that is not performing well, reallocating staff to address performance issues or identifying expiring products and waste.
How to choose the right warehouse management system
A modern warehouse management system will support your business as it grows and changes into the future. You will want to find a system that offers low overall risk. This means you can get up and running quickly on the system via a rapid implementation model and can make software changes over time to meet new challenges. This adaptability is a critical factor in molding the system to your specific customer or industry requirements where appropriate.
Finding a system that is ‘future proof’ is also important. Not only do you need core functionality to be in place today, but you also need to be able to stay on the upgrade path down the road as new enhancements are released and you want your warehouse management system to keep pace.
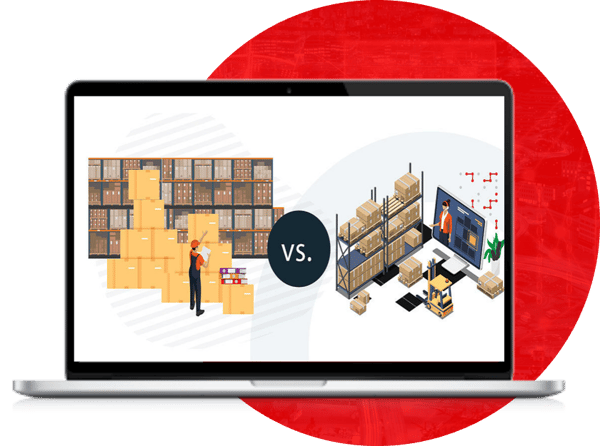
Check out why it might be time to find a modern WMS with the functionality necessary to meet your needs in today's world.
get infographicTraditional WMS vs. modern WMS
Hardware
Traditional: Large ‘brick on a stick’ mobile terminals with physical buttons.
Modern: Familiar smartphone or tablet devices running Android or iOS.
Adoption
Traditional: Long and complex implementations, formal training sessions run by the vendor.
Modern: Low risk and rapid to adopt, uses familiar technology which improves user experiences with user-driven training and configuration.
Flexibility
Traditional: Any changes to the standard process require custom coding that makes upgrades expensive and difficult.
Modern: Features and workflows can be adapted using scripts, configurations and workflow management tools by super users who are semi-technical and do not require developers.
Scalability
Traditional: Limited by the hardware and network locally available, once set is generally fixed.
Modern: Totally elastic solution for any size implementation; can flex along with seasonality requirements throughout the year as needed.
Features
Traditional: Feature set is basic receive, putaway, letdown, count and pick.
Modern: Industry or process-specific features that are configurable by the role of the user.
Platform
Traditional: There isn’t one.
Modern: The supply chain platform creates a common, stable and personalized environment that allows user-centric change to the look and feel of the system without affecting the underlying solution. It also provides an integration layer to simply and rapidly connect.
Review these nine modern warehousing methods and practices to ensure you have all your bases covered on your warehouse optimization journey.
What are the benefits of a cloud warehouse management system?
7 key steps to implementing warehouse management systems
Step 1: Identify
The most important part of any project is to figure out what are the key problems you need to solve and which technology partner has the most relevant experience that fits your company culture best.
Step 2: Initiate and Plan
Introduce and explain the nuances of your operation to your technology partner and plan the end-to-end project — understand both the staffing and timeline.
Step 3: Analyze and Design
Define with your partner how your new system will work, making sure all the key processes and integration steps are well documented and understood. Start to collect and cleanse the master data needed to run the system.
Step 4: Build the Solution
Create the solution configuration, load the master databases, build the integration, train the internal subject-matter experts and create the test plans.
Step 5: Validate
Check everything and test how your system will operate. Closely examine the integration, stress test the system and train the users by doing some dry runs. Finally, decide if you are ready to go-live!
Step 6: Deploy
When you are ready to go-live, transition to the new system and possibly do an inventory count. And do not forget to support the users through the learning phase.
Step 7: Review
Complete a retrospective review post-implementation and create optimization plans to support your continuous improvement processes.
Future of warehouse management
Warehouse management is at a nexus point where the industry is moving away from gradual evolutionary steps that improve the warehouse management processes to truly revolutionary change in the warehouse and the technology that runs it. The changes are brought on by the increase in complexity and volume of transactions in the warehouse over the last few years — and that rate of change is only accelerating. This, along with the shortage and increasing cost of labor, has meant that automation and AI techniques are increasingly being applied to the traditional warehouse management system.
Automation in the form of collaborative robots all the way to complex automated storage and retrieval systems like AutoStore are being adopted to address these transaction, volume and labor issues. In addition, warehouse management systems are getting smarter and applying machine learning technology to do the tasks needed to make the warehouse floor the most efficient. Jobs like cluster building, task management and pick allocation are all being managed in real time, revised dynamically by AI in ways that will build efficiency and change the warehouse floor operation forever.
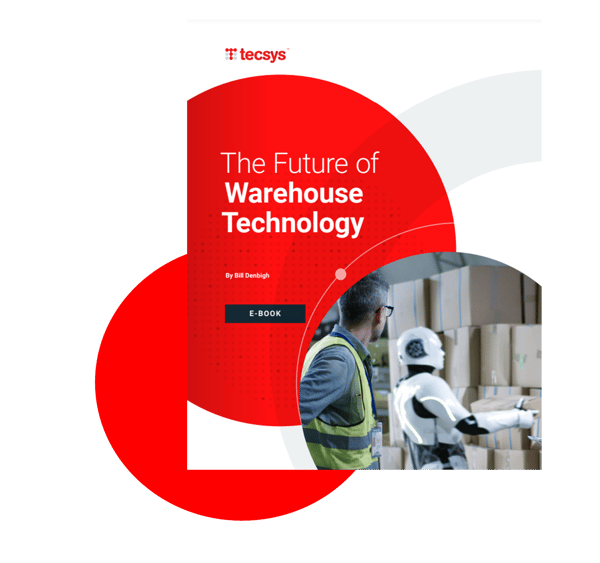
This e-book will guide you through the next major advancement in the warehouse and its benefits to efficiency, usability and accuracy.
Get e-bookElite™ warehouse management system
Tecsys’ Elite™ WMS is a visionary, scalable and adaptable solution that addresses the complexity and economic challenges of distribution operations in several industries to help you keep pace with a shifting landscape and move forward confidently.
Your warehouse operation is your most vital asset to deliver on promises made to customers and achieve a high level of customer satisfaction. In today’s world, a combination of best practices and platform technology helps world-class distribution organizations achieve market differentiation, eliminate inefficiencies, improve order accuracy, reduce operating costs and attain high levels of service. Undoubtedly, your warehouse is more critical than ever.
For more than four decades, we have helped hundreds of leading organizations solve their unique warehousing and distribution challenges — landing us in the Gartner Magic Quadrant for Warehouse Management Systems for 13 consecutive reports, positioned as "Challenger" since 2022.
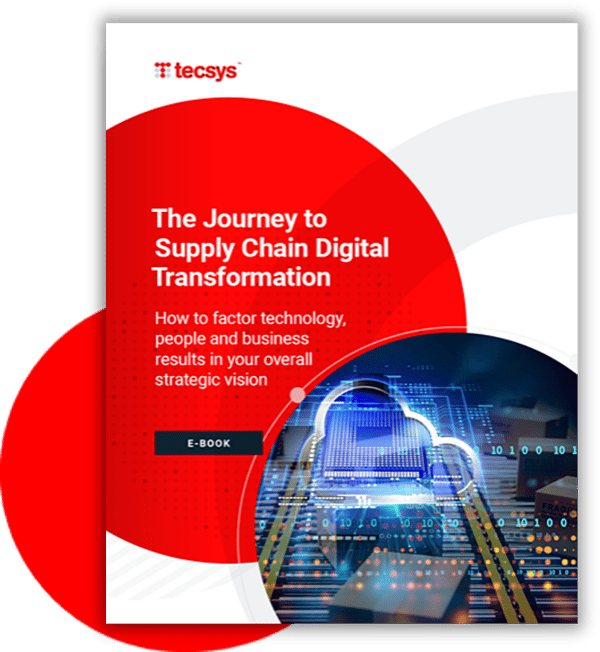
Access this e-book to gain insights from digital transformation experts on how to get your infrastructure right and enable your organization to build a competitive supply chain well into the future.
get e-book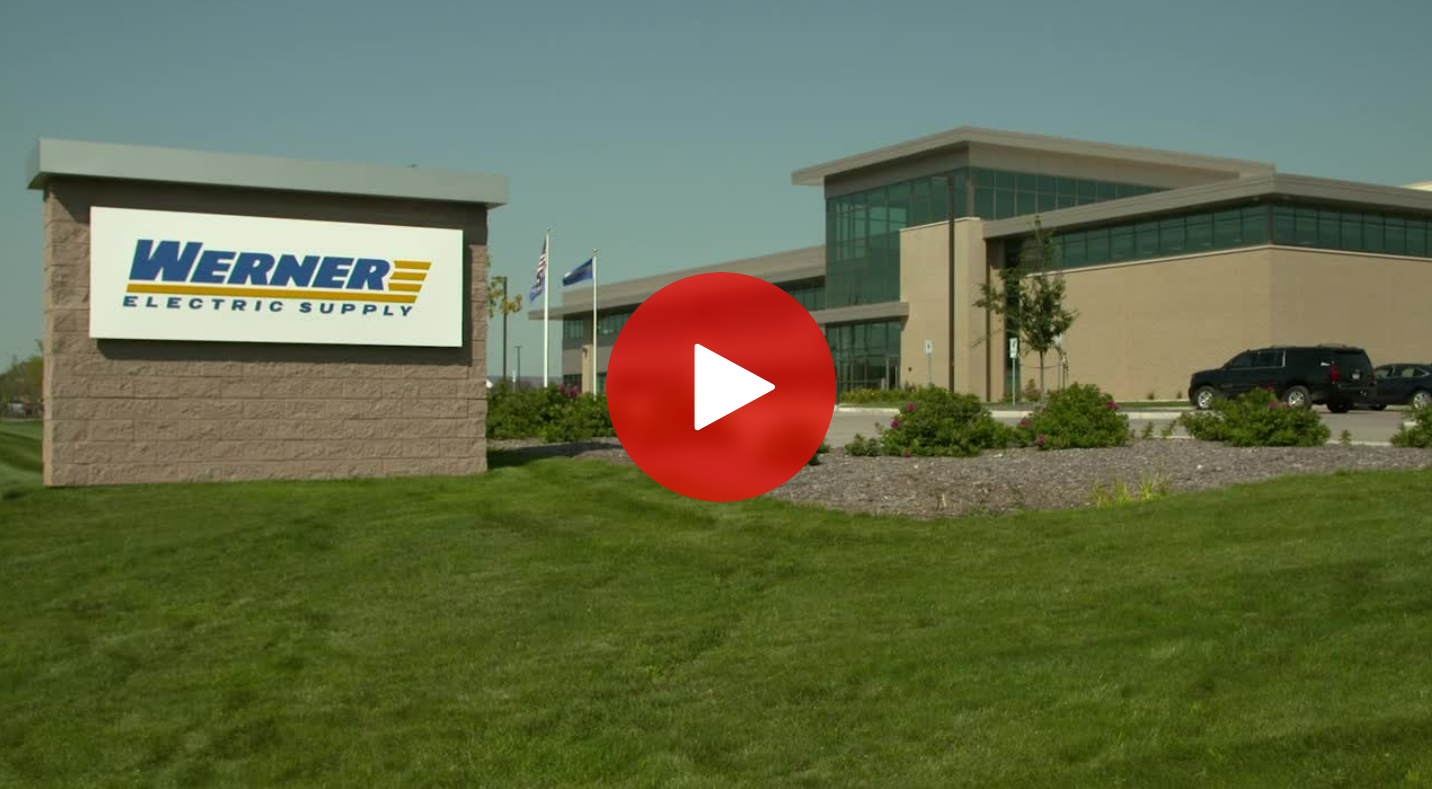
Advanced core warehouse management functionality
Elite™ WMS provides advanced functionality for receiving, putaway, inventory moves, picking, packing, replenishment, shipping, loading and cycle counting. This helps ensure that all your warehouse operational requirements are met.
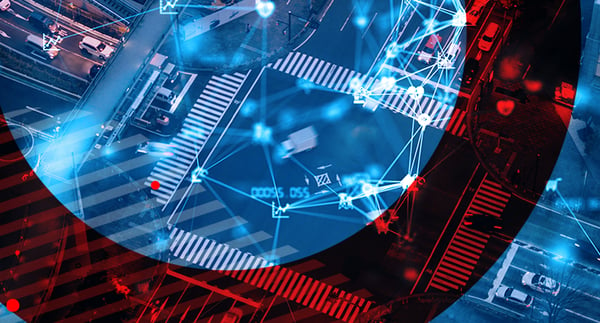
System-directed RF task management and task interleaving
With system-directed RF task management and task interleaving, the Elite™ WMS removes the complexity and inefficiency of your material handlers picking their next task or being assigned to only perform a single task in the warehouse. Customers have increased efficiency and accuracy by double digits at the lowest possible operating cost.
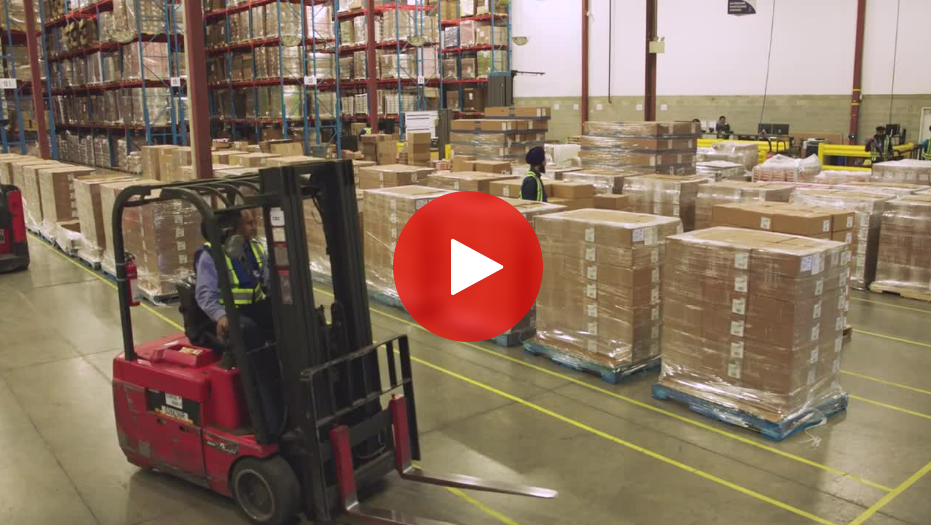
Multiple pick methods
Tecsys’ Elite™ WMS picking methods include wave, waveless, zone, batch, cluster and user-defined and can be combined to make your most labor-intensive process the most efficient possible. By leveraging flexible and modifiable workflows, your warehouse can do more with less and eliminate errors.
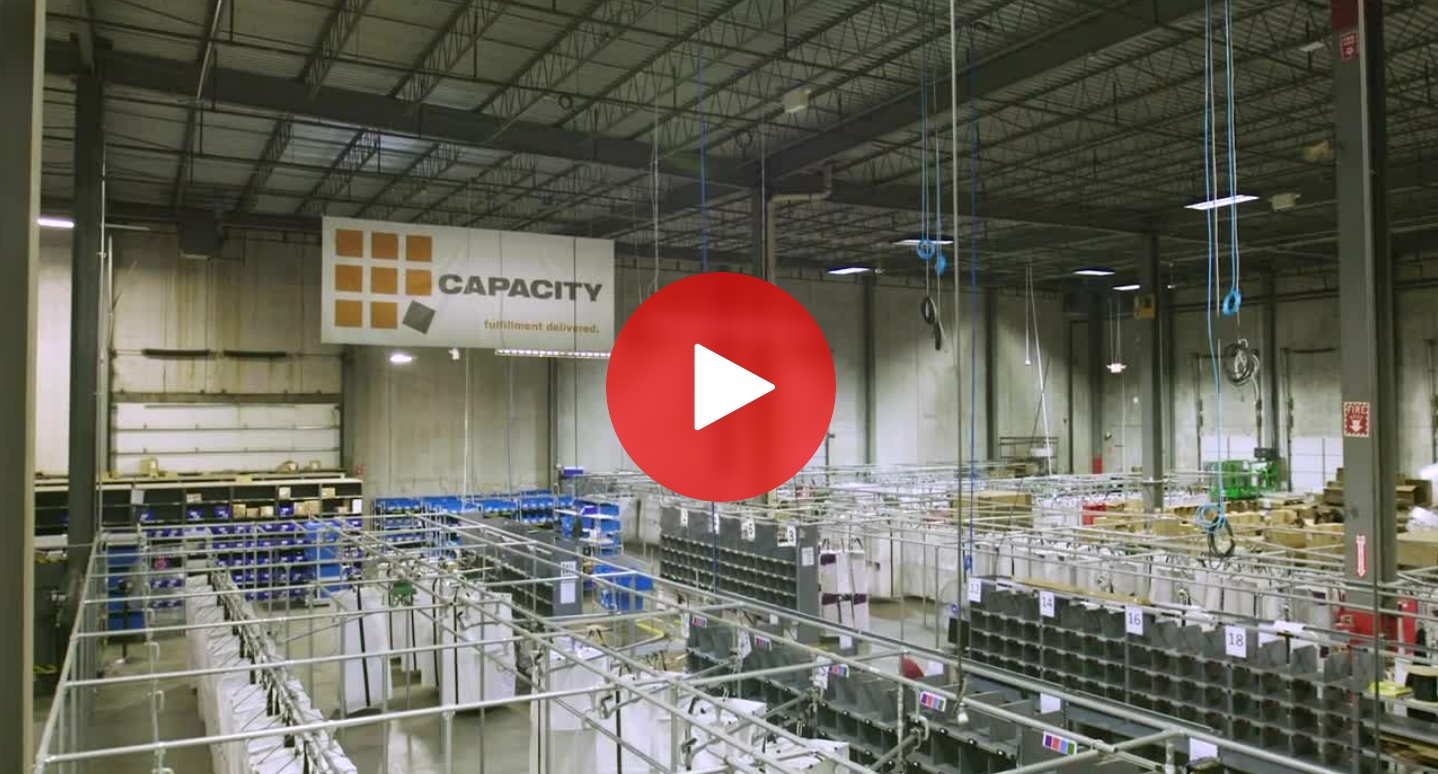
Volumetrics and containerization
Understanding the exact dimensions of everything in the warehouse and managing what can go where, what will fit in what container and the best use of your space is the starting point for warehouse optimization. Your Tecsys Elite™ WMS will track and manage the use of space throughout your warehouse for the most optimized and efficient workflows using complex volumetrics algorithms. Volumetrics functions include ensuring the product will fit in the storage slot before recommending it to the material handler, suggesting the right sized shipping container to pick into and recommending the correct warehouse locations for products based on their usage and activity all add to the smooth running of the facility.
Embedded advanced transportation management functionality
At Tecsys, we always say that you do not need a TMS, but you do need a WMS that knows how to ship. Tecsys’ Elite™ WMS can be easily integrated with our Elite™ TMS solution to allow your warehouse planning process to take the shipping method into account, pick into the ultimate shipping container and handle shipping exceptions before they become problems.
Aetrex
Aetrex is widely recognized as the global leader in comfort and wellness footwear. Originally known for the landmark development of arch supports and medically oriented footcare products, Aetrex has come a long way to become one of the leading footwear companies in the U.S. and around the world. To meet its goal of becoming a major brand in footwear, fast-growing Aetrex needed a strong supply chain infrastructure to support its go-to-market strategy and provide its management and customer service staff with the right information to better serve clients and distributors.
Aetrex selected Tecsys’ warehouse, distribution management and EDI applications to support its goals. The company chose Tecsys due to its unparalleled customer care and responsiveness as well as the strength of its applications. Since implementing Tecsys’ solutions, Aetrex has grown at an aggressive rate and achieved its strategic sales and customer service goals. The results speak for themselves: Aetrex has increased volume by 80% without additional staff, increased inventory accuracy by 70% and reduced cost by 24%.
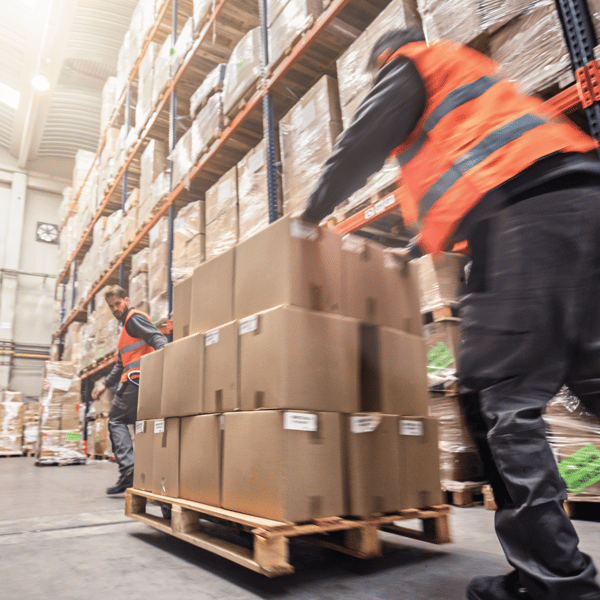
"At the end of the day, with Tecsys we are now miles ahead in our execution abilities and management of our supply chain." - John Mattessich, Director of Distribution
Read Success StoryLifeScience Logistics
LifeScience Logistics (LSL) is a third-party logistics services provider in the healthcare industry. The company provides a full range of standard and specialized logistics services scalable to the changing needs of its customers. LSL faced the challenge of providing domestic and global healthcare manufacturers with unique, regulatory compliant distribution facilities and processes. They chose Tecsys’ healthcare SaaS (Software-as-a-Service) model, and the results have been impressive.
LSL has achieved substantial automation with Tecsys’ supply chain management solutions such as scalable, perpetual inventory, significant improvement in labor management with system-directed putaway and picking, as well as unprecedented real-time visibility. The company has also realized the following benefits: 99% fill rates and 99.97% inventory accuracy with the right products delivered at the right price without sacrificing quality.
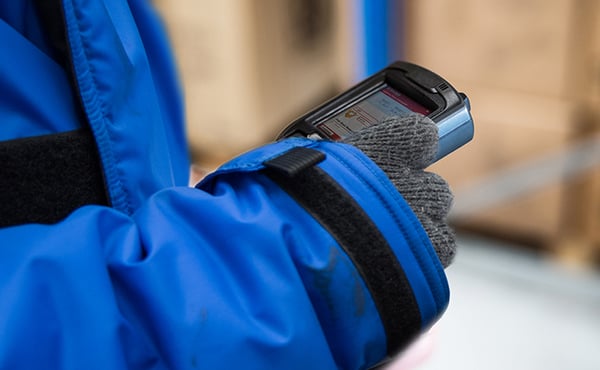
"We have a reliable IT infrastructure that can be tapped anytime, from anywhere, securely … it is like “googling” into a supply chain network of applications, giving us and our customers peace of mind and visibility of what is happening…" – Richard Beeny, Co-founder and Chief Executive Officer
Read Success StoryJoin the new class of industry leaders and revolutionize your supply chain
Tecsys doesn’t just support your supply chain; we help transform businesses from good to great. Join our customers and build a new kind of supply chain.
The farming industry is a precarious one, and those who serve it need to be as efficient as possible; Abilene Machine uses Tecsys to reduce inventories without negatively impacting customer service or production scheduling.
Growth in revenue
Reduction in inventory
Increase in revenue by employee
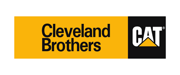
As one of the largest Caterpillar dealers, Cleveland Brothers needed to support both management and distribution, but also provide staff with real-time visibility and tracking. Tecsys’ Elite WMS has made this possible, and more.
Increase in order accuracy
Savings in labor costs
Fill rate
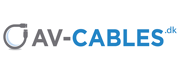
Rapid growth in e-commerce has impacted many industries, but distributors and retailers are working tirelessly to manage their supply chain operations. Management teams across the board are struggling to balance rising logistics costs as orders continue to increase.
Increase in order capacity
items to dispatch daily
implementation
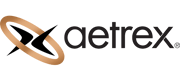
With ambitious goals in mind, footwear manufacturer Aetrex turned to Tecsys' warehouse management system to become a global leader in orthopedic footwear.
Increase in volume
Increase in inventory accuracy
Reduction in costs
The farming industry is a precarious one, and those who serve it need to be as efficient as possible; Abilene Machine uses Tecsys to reduce inventories without negatively impacting customer service or production scheduling.
Growth in revenue
Reduction in inventory
Increase in revenue by employee
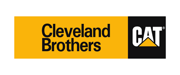
As one of the largest Caterpillar dealers, Cleveland Brothers needed to support both management and distribution, but also provide staff with real-time visibility and tracking. Tecsys’ Elite WMS has made this possible, and more.
Increase in order accuracy
Savings in labor costs
Fill rate
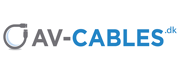
Rapid growth in e-commerce has impacted many industries, but distributors and retailers are working tirelessly to manage their supply chain operations. Management teams across the board are struggling to balance rising logistics costs as orders continue to increase.
Increase in order capacity
items to dispatch daily
implementation
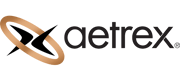
With ambitious goals in mind, footwear manufacturer Aetrex turned to Tecsys' warehouse management system to become a global leader in orthopedic footwear.
Increase in volume
Increase in inventory accuracy
Reduction in costs
The farming industry is a precarious one, and those who serve it need to be as efficient as possible; Abilene Machine uses Tecsys to reduce inventories without negatively impacting customer service or production scheduling.
Growth in revenue
Reduction in inventory
Increase in revenue by employee
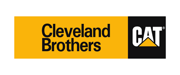
As one of the largest Caterpillar dealers, Cleveland Brothers needed to support both management and distribution, but also provide staff with real-time visibility and tracking. Tecsys’ Elite WMS has made this possible, and more.
Increase in order accuracy
Savings in labor costs
Fill rate
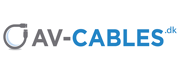
Rapid growth in e-commerce has impacted many industries, but distributors and retailers are working tirelessly to manage their supply chain operations. Management teams across the board are struggling to balance rising logistics costs as orders continue to increase.
Increase in order capacity
items to dispatch daily
implementation
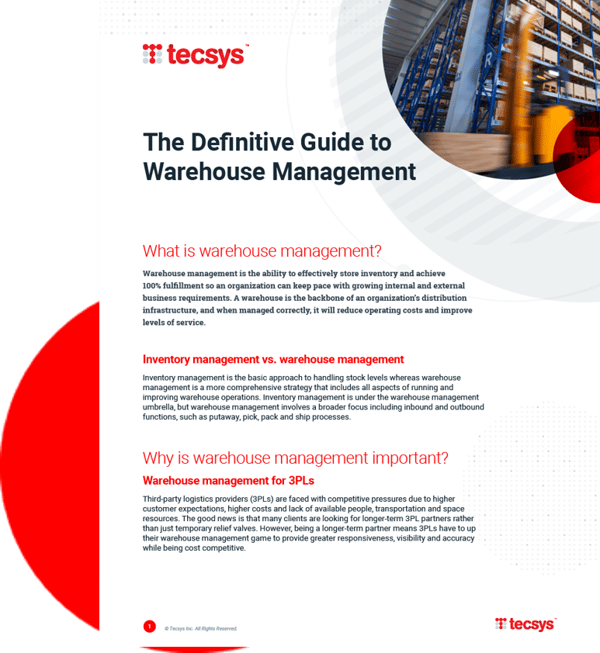
Access the definitive guide to learn the principles, strategies and solutions for effective warehouse management.
get e-book